Insights
Dissolved Gas Analysis for Power Transformers: A Smart Approach to Asset Management
April 24, 2025Power transformers are the heart of electrical transmission systems, converting high-voltage electrical power into a usable form for consumers. However, the reliability and longevity of these critical assets are often threatened by hidden faults that can lead to catastrophic failures, costly repairs or even prolonged downtime.
Dissolved Gas Analysis (DGA) is an invaluable tool in transformer maintenance and fault prediction. By leveraging advanced DGA technologies, utility companies and industries can stay ahead of potential issues, reducing both capital and operational expenditures while ensuring the continued health of their transformer fleets.
What is Dissolved Gas Analysis?
At its core, DGA involves analysing the gases that are dissolved in the oil inside power transformers. These gases are released when the oil and insulation materials inside the transformer are stressed due to high load, faults or normal operating conditions.
As these stresses break down the insulating oil and paper, specific gases are produced. These gases dissolve into the transformer’s oil, where they remain until analysed.
By measuring the concentration of these gases, DGA provides critical insight into the transformer’s health and helps identify potential faults before they escalate.
Why DGA Matters for Power Transformers
Power transformers operate under extreme conditions that can take a toll over time.
When issues such as overheating, partial discharge or arcing occur, DGA can detect the gases generated from these events and indicate the severity of the fault. This allows for early diagnosis, preventing expensive unplanned maintenance or, worse, complete transformer failure.
As transformer fleets age, the risks associated with potential faults increase. With the growing pressure on utilities and industries to manage their assets more efficiently and minimise costs, DGA has become an essential tool for proactive asset management.
It’s a powerful way to monitor the condition of transformers and predict potential failures before they become a serious problem.
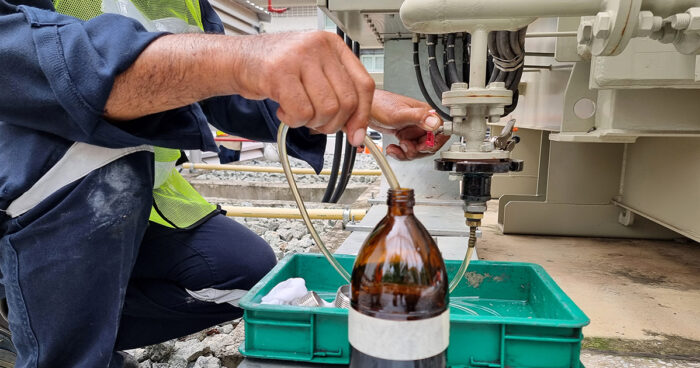
The Power of Real-Time Monitoring
The true strength of modern DGA systems lies in their ability to provide real-time monitoring. Systems like the Hydran M2-X and the Intellix BMT 330 can now conduct full 9-gas analyses multiple times a day, completely autonomously. These systems are designed to be integrated into the transformer’s existing monitoring network, allowing operators to remotely track the development of gases over time.
Remote monitoring means no more waiting for annual lab tests to reveal a developing fault. Instead, utilities can detect trends and anomalies as they happen, allowing for immediate intervention if necessary. This reduces downtime and prevents further damage to critical infrastructure.
How DGA Reduces Operational Costs
Traditionally, DGA required costly site visits and lab testing, which only happened once a year due to high cost and logistics involved. As a result, minor issues could develop over long periods without detection, leading to more extensive damage.
With continuous DGA monitoring, faults are detected early, before they can cause substantial harm.
In addition, real-time results allow utilities to take action promptly, reducing the need for emergency repairs and the risk of expensive transformer replacements. It also leads to more efficient maintenance schedules, meaning that only critical components require attention, reducing labor and logistics costs associated with routine inspections.
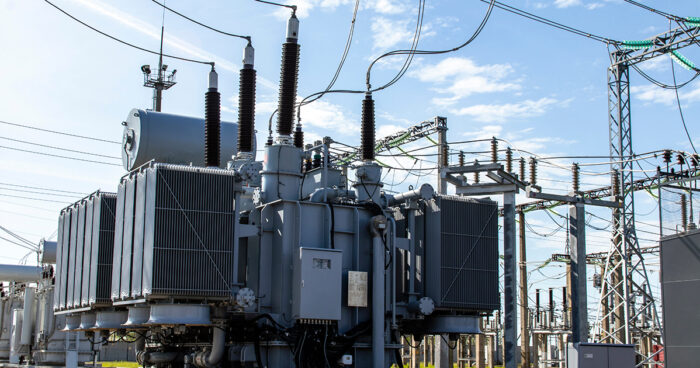
Safety and Reliability with DGA
One of the key benefits of DGA is its safety impact. Traditional fault detection methods required the use of high-pressure gas cylinders for testing, which could be hazardous in substation environments. DGA removes this risk by enabling remote monitoring without the need for additional hazardous equipment onsite.
The rugged nature of modern DGA units also ensures they can operate reliably in harsh environments, withstanding mechanical shocks, temperature fluctuations and vibrations commonly found in substations.
Discover the Benefits of DGA for Transformers
As utility companies seek smarter, cost-efficient systems, DGA is becoming essential for transformer fleet management. With real-time, autonomous monitoring and data analytics, DGA enhances transformer reliability and extends lifespan.
Key benefits of DGA include:
- Autonomous operation: DGA conducts gas analysis multiple times a day, automatically, without user intervention.
- Reliable in all conditions: Immune to environmental factors like temperature, noise and vibration, DGA ensures accurate readings over extended periods.
- Improved safety: Remote monitoring reduces the need for hazardous gas cylinders, enhancing worker and plant safety.
- Durability: DGA devices are rugged, compact and insensitive to mechanical shock or vibration, requiring minimal temperature control.
At CSE Uniserve, we are proud to offer a range of industry-leading DGA solutions like the Hydran M2-X, Intellix BMT 330, and CB Watch 3.
Reach out to our team to see how DGA can work on your site.